鍛造工藝是一種常見的加工技術,經常利用鍛壓機使需要被鍛造的材料由于受到壓力而變形從而使原始的金屬零件轉化成為需要的尺寸和狀態,鍛造主要包含兩種類型,即鍛造和沖壓。
鍛造產生的金屬鍛件具有良好的性能,主要由于鍛造增加了金屬原材料的密度,避免其結構疏松造成的不穩定,除此之外,其保證了金屬鍛件產生的性能,因此被廣泛用于目前的零件加工產業。這些鍛造零件可以應用于某些工作環境苛刻的設備中,可以有效抗負載,具有極高的穩定性,因此鍛件的應用前景廣闊。
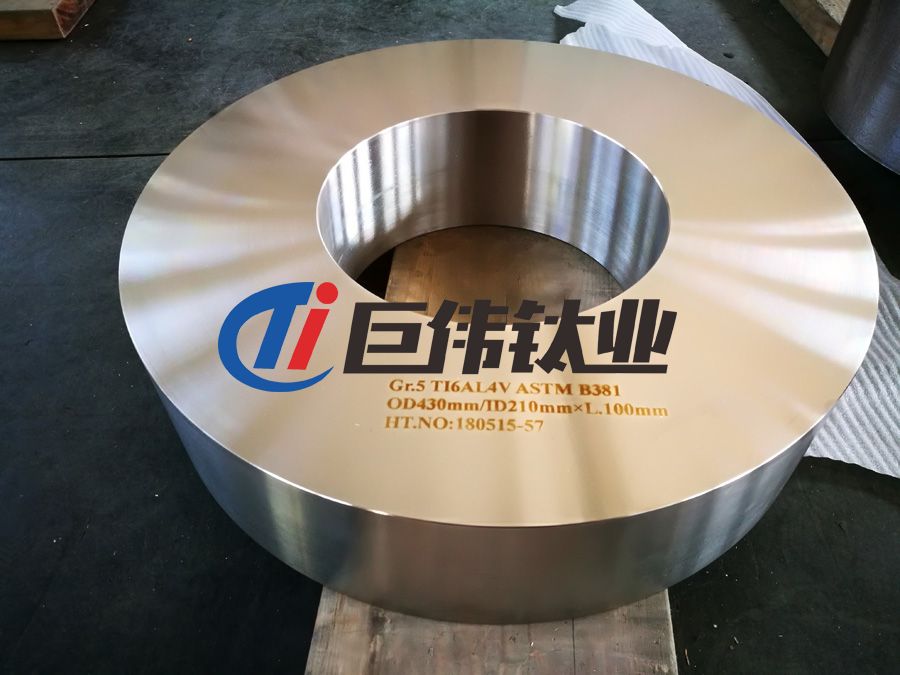
鈦合金是一種新型的合金[1],其主要是增加了鈦金屬的強度,同時降低了鈦金屬的密度,從而保證鈦金屬具有優秀的耐腐蝕性能,因此有很大的應用價值。為了更好地應用這些材料,鍛造工藝對鍛件性能影響的研究十分必要。鍛造是利用金屬的塑性[2],在工具的沖擊或壓力下,獲得具有特定形狀和結構性能的塑性成形工藝。鍛造生產的優勢在于,不僅可以獲得機械零件的指定形狀,而且可以改善材料的內部結構,提高機械零件的機械性能。鈦合金鍛件廣泛用于制造中溫發動機風扇和壓縮機葉盤。
利用鈦合金鍛件可以有效地將葉盤的結構類型轉化,由傳統的多連接葉盤轉化成葉片圓盤連接型葉盤[3],這樣可以導致整個葉盤的結構不那么繁瑣,組成葉盤的材料需求也降低了,因此葉盤此時能進行保形配置,葉盤需要更好地低疲勞和抗蠕變配置。因此,本文研究了鍛造工藝對鈦合金鍛件組織和性能的影響。
1、試驗方案
1.1 整體葉盤形狀與尺寸
研究的鈦合金選用TC17 合金,該鈦合金的是 (Mo+Cr) 含量為8%,比TC4 和Ti-6242 具有更高的中溫強度,因此現在被廣泛地使用在其中。發動機風扇和壓縮機集成葉盤制造可以使用鈦合金鍛件來有效地轉化葉盤的結構類型,使其結構由繁到簡,不僅減少了葉盤再制造生產時需要的工序,也降低制造葉盤的材料消耗。由于葉盤在使用過程中必須保證時刻具有彈性,因此必須要避免其由于疲勞產生的不可彎曲的問題。研究表明,葉盤的疲勞問題主要由葉盤的鍛造方式來改善,在鍛造時可以增加其紋理狀態太保證性能。葉盤組織受熱導致其性能轉變的臨界點溫度即為葉盤鍛造時需要注意的變形溫度,根據葉盤加熱變形溫度得出固定的組織,該組織稱之為三相組織,以上階段的鍛造稱為近β 鍛造。與該過程不同,葉盤組織使用極高的溫度加熱后,導致其性能完全受到損傷,甚至產生層狀結構的過程稱為β鍛造。研究表明,本實驗研究的鈦合金TC17,使用這兩種鍛造方法鍛造出的網籃三相結構更能滿足飛機發動機的技術要求。
首先,應明確檢測整體葉盤鍛件的盤形和尺寸,如圖1 所示。
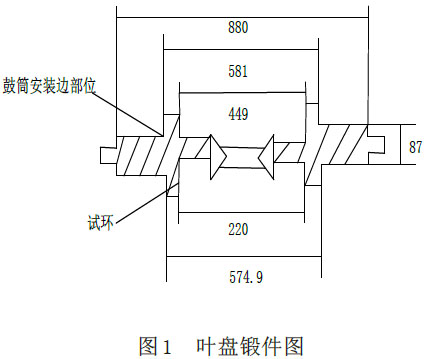
如圖1 所示,整個葉盤鍛件由試環和鼓筒安裝邊部位組成。
1.2 原材料
本試驗選用310mm×80mm 的TC17 合金,該合金的化學成分能為:5.12Al、4.14Cr、4.06Mo、2.17Sn、1.98Zr、0.01C、0.005N、0.0021H,β 相轉變溫度Tβ 為893℃。試驗用料是經過相變點下多次鐓拔變形的均勻雙態組織。
1.3 工藝設計
為了對比TC17 合金近β 鍛和β 鍛后組織性能,設計了如下鍛造工藝路線。
第一種,坯料加熱(Tβ+25) ℃,等溫鐓粗,變形速度v=1mm/s,等變形量55%,鍛后空冷,熱處理采用800℃ ×4h,WQ+630℃ ×8h,AC。
第二種,坯料加熱(Tβ-20) ℃,等溫鐓粗,變形速度v=1mm/s,變形量40%,鍛后水冷,熱處理采用850 ℃ ×3h,AC+800℃ ×4h,WQ+630℃ ×8h,AC。
這兩種工藝方案主要的區別在于其相變點的加熱方式,以一種選用了相變點上加熱,第二種則選用相變點下加熱,兩者鍛后也不一樣,第一種鍛后選擇空冷,第二種則是水冷,熱處理為均勻化+ 固溶+ 時效。
1.4 試驗過程
在試驗過程中,首先需要將原材料進行改鍛,改鍛的環境控制在3t 范圍內,由于改鍛的過程可能會發生其他類型的反應,因此需要預先設置改鍛的尺寸,本文采用的鍛錘為常規鍛錘,需要將改鍛尺寸設定為250mm×120mm,尺寸輸入后需要進行改鍛的加熱處理,本試驗選取電爐進行加熱處理,設置電爐的探波數值,進行預熱處理后即可開始進行改鍛。
1.5 試驗取樣圖
根據試驗過程,選取試樣的部位進行試驗取樣,試驗取樣圖如圖2 所示。
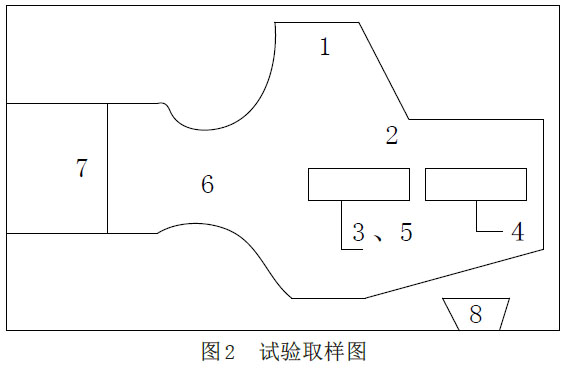
由圖2 可知,試樣取樣分成若干步驟,不同的鍛造工藝試驗取樣的位置也不同,圖中的1、2 位置為熱穩定取樣,5、6、7、8均為高溫拉伸取樣,4 代表疲勞取樣。
2、試驗結果與討論
2.1 不同鍛造工藝對顯微組織的影響
如圖3 所示,為近β 鍛工藝鍛件的顯微組織。其初生α 含量約20%,條狀α 沿原始β 晶界分布,原始β 晶粒尺寸較小,晶界基本破碎,為等軸α+ 條狀α+β 狀的三態組織。
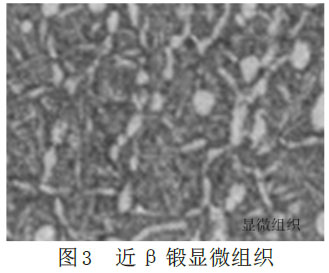
圖4 為β 鍛顯微組織圖,該顯微組織可以反映相變點的熱變形量,經過研究證明,其在某個固定溫度可以導致鍛造變形,從而使顯微結構發生轉變。
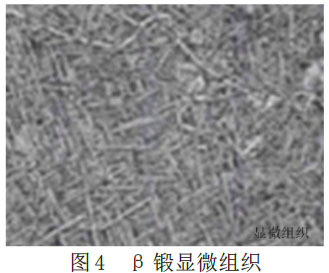
由圖4 可知,試驗中的鈦合金普遍都可以經過鍛造產生網籃反映,經過鍛造后的鈦合金顯微結構呈現出網狀,容易受熱改變性質,因此證明此時滿足鍛造條件。
2.2 不同鍛造工藝對力學性能的影響
分別使用兩種不同的鍛造工藝,即近β 鍛和β 鍛,根據這兩種鍛造工藝進行性能檢測,分別檢測室溫拉伸,高溫拉伸和熱穩定狀態下兩種鍛造方式的性能差異,由于鍛造工藝受到金屬本身的性能影響,因此需要提前進行熱處理才能進行后續試驗,檢測結果如表1~3 所示。
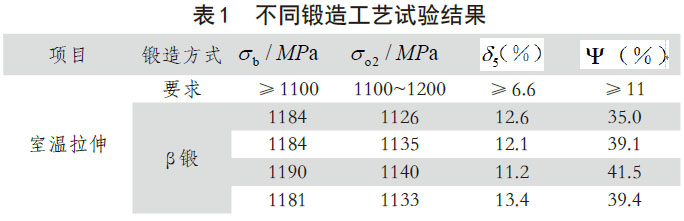
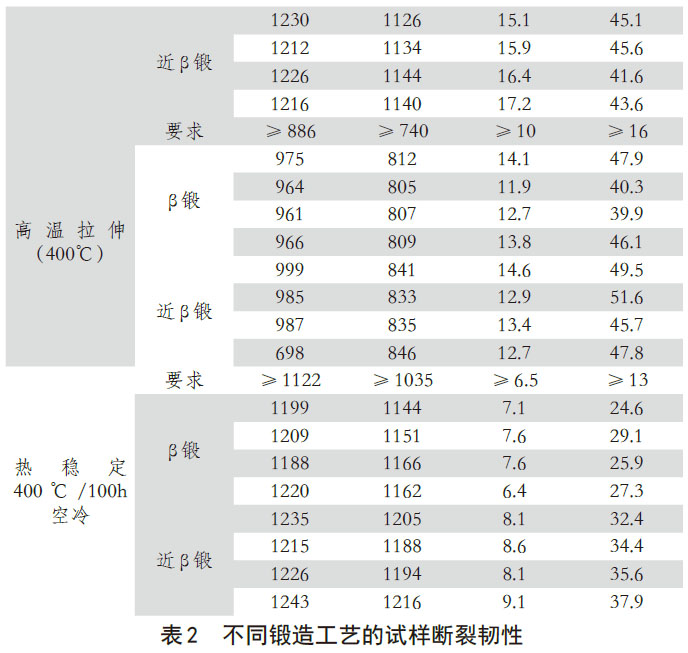

由表1~ 表3 可知,兩種工藝的力學性能有較大差異,主要體現在斷裂韌性方面,近β 鍛的斷裂韌性相對于β 鍛來說偏小,比較容易由于受到某些刺激而產生斷裂,而β 鍛就比較穩定,不容易發生斷裂,因此β 鍛比近β 鍛的性能高,適合應用于葉盤的制造中,除此之外,進行抗疲勞試驗也是為了檢測二者的性能差異,計算二者的最大疲勞樹脂。傳統兩相鈦合金網籃組織高周疲勞較差,但TC17 合金網籃組織的疲勞極限強度可比較高,因此可以用作葉盤的生產材料。
3、結論
β 鍛工藝的鍛件強度、塑性及斷裂韌性等綜合力學性能較好,近β 鍛工藝的斷裂韌性較差,因此鈦合金發動機葉盤應選用β 鍛造工藝鍛造。
4、結語
綜上所述,鈦合金鍛件在航空航天,醫療方面有重要應用,其具有耐腐蝕,高強度的優勢,研究表明,近β 鍛雖然強度和塑性優于β 鍛,但其斷裂韌性較差。TC17 合金整體葉盤鍛造應選用β 鍛工藝,對后續鈦合金的應用有一定的參考價值。
參考文獻
[1] 白東輝, 湯育璽. 鍛造工藝對TC17 鈦合金鍛件組織性能的影響[J]. 熱加工工藝,2020,49(23):84-86.
[2] 楊華, 高俊峰, 何琪功等. 徑向鍛造機的幾種典型主機結構分析[J]. 鍛壓技術,2021,46(06):16-32.
[3] 闞海波, 呂興龍, 李偉華等. 耐極寒OPGW 金具鍛造與熱處理工藝性能研究[J].電力信息與通信技術,2019,17(08):63-69.
相關鏈接