鈦是一種新金屬,它具有密度小、比強度高、耐蝕性好,加工性及焊接性好的優(yōu)點,還具有較好的耐熱性和耐低溫性能,被廣泛地應用于航空航天、石化、冶金、電力、輕工及艦船等各個領域,在汽車工業(yè)中也得到了一定的應用。但是由于鈦合金價格昂貴,在一般民用品上的應用還很少,鈦合金在汽車工業(yè)中的應用也大多在豪華車型和跑車上,目前的賽車幾乎都使用了鈦材。展望未來汽車工業(yè)的發(fā)展方向,輕量化、油耗低及排放少是發(fā)展的主題。盡管目前高強度薄鋼板、鋁材、鎂材、金屬基復合材料及塑料樹脂類材料在減輕汽車整備質量方面已經(jīng)發(fā)揮了作用,隨著工業(yè)水平的發(fā)展及世界對環(huán)保節(jié)能要求的日益提高,鈦合金在普通家用汽車上的使用也會得到快速發(fā)展。
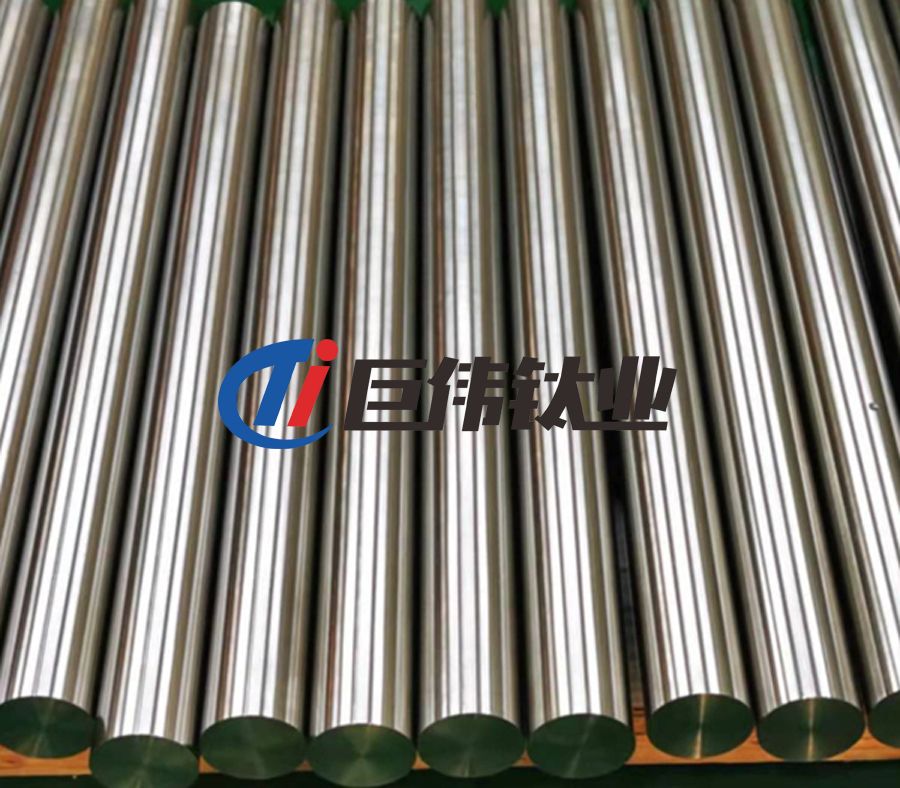
一、鈦合金在汽車工業(yè)的應用現(xiàn)狀
雖然鈦元素早在18世紀末即被英國和德國的科學家發(fā)現(xiàn),但是直到20世紀初美國的科學家才提取出了純鈦,鈦的工業(yè)化規(guī)模生產(chǎn)已經(jīng)是1948年的事情了,鈦工業(yè)的發(fā)展是伴隨著航空航天工業(yè)的發(fā)展而發(fā)展起來的新興產(chǎn)業(yè)。盡管鈦合金在在航空航天、石油化工、艦船工業(yè)上的應用已很廣泛,但是在汽車工業(yè)中的應用卻發(fā)展緩慢。從1956年美國通用公司研制成功第一輛全鈦汽車開始,直到20世紀80年代,鈦制汽車零部件才達到批量生產(chǎn),90年代隨著豪華汽車、跑車、賽車需求量的逐年增加,鈦制零部件才得到了加速發(fā)展。
鈦材作為汽車部件材料使用的優(yōu)點有:強度高、密度小、彈性模量約是鋼的一半,熱膨脹系數(shù)低,約是不銹鋼及鋁材的一半,無磁性、熱導率低、對環(huán)境無污染等。另外在汽車行業(yè)用鈦后,可極大減輕汽車整備質量,降低其燃料消耗,提高汽車工作效率,降低噪聲。最常見的是利用鈦合金制造發(fā)動機零件,有很多好處:鈦合金的密度低,可以降低運動零件的慣性質量;同時鈦氣門彈簧可以增加自由振動,減弱車身的振顫,提高發(fā)動機的轉速及輸出功率;減小運動零件的慣性質量,從而使摩擦力減小,提高發(fā)動機的燃油效率。選擇鈦合金可以減輕相關零件的負載應力,縮小零件的尺寸,從而使發(fā)動機及整車的質量減輕。零部件慣性質量的降低,使得振動和噪聲減弱,改善發(fā)動機的性能。綜合起來,鈦合金在汽車產(chǎn)品上的用途主要分為兩大類,第一類是減少原有零件的質量,涉及零件主要有發(fā)動機的高速往復運動件和汽車自重。第二類是用來制作耐腐蝕件,主要包括排氣系統(tǒng),底盤零件,懸架系統(tǒng)等所處環(huán)境惡劣的汽車零部件,可提高汽車零件的使用壽命。
隨著社會發(fā)展,節(jié)能環(huán)保是產(chǎn)品發(fā)展主體,汽車“輕量化”是汽車行業(yè)一項非常重要直接的節(jié)能減排措施,目前已成為行業(yè)的共識。研究表明,汽車所用燃料約60%消耗于汽車自重,汽車每減輕10%的整備質量,廢氣排放量可減少10%,可降低油耗7%。1956年,通用汽車公司(GM)和其供貨商裝配了一種展覽用的小汽車,其車體是全鈦;日本本田汽車公司1994年在NSX賽車3.0L24閥V-6發(fā)動機中使用鍛造鈦連桿;三菱汽車公司制造的高容量、四缸發(fā)動機中使用了鈦氣門彈簧座;保時捷汽車中也使用了鈦連桿。隨著鈦的日益發(fā)展,在汽車上的特殊用途已大量應用到高級車零部件上(見表1)。
目前常用的鈦合金零部件比較多,主要對以下幾種詳細介紹。
表1 鈦制汽車標準部件的應用狀況

1、發(fā)動機連桿
連桿連接活塞與曲軸,起著傳遞動力的作用,承受著很大的沖擊力,因此連桿必須有足夠的強度,并且質量要盡可能輕,以提高發(fā)動機的轉速。連桿連接活塞與曲軸,將活塞的動力傳遞到曲軸,因承受很大的沖擊力,故必須強度大且不易變形。此外,連桿也必須質輕,以減少慣性損失,提升發(fā)動機最高轉速。鈦合金是理想的連桿用材料。
鈦合金連桿常用的材料為Ti-6Al-4V鈦合金,Ti-6Al-4V鈦合金于1954年在美國研究成功,首先用于航空航天業(yè),它具有良好的強韌性、優(yōu)良的加工性和耐腐蝕性。1987年本田公司的VFR750R型車最先采用Ti-6Al-4V鈦合金連桿進行批量生產(chǎn)和銷售,但Ti-6Al-4V鈦合金價格較昂貴,對其推廣使用有一定的難度。后研發(fā)出Ti-3Al-2.0V鈦合金連桿,用在了Accura NSX 3.0升V6 發(fā)動機上,與鎳鉻鋼連桿比較,Ti-3Al-2.0V鈦合金連桿可節(jié)省30﹪的質量且有相等的疲勞強度。Ti-3A-2.0V 價格較Ti-6Al-4V 便宜,Ti-6Al-4V 與Ti-3Al-2.0V有相同的Al/V 比,故能由回收的Ti-6Al-4V 中制造Ti-3Al-2.0V,且因質量減輕,慣性損失少,故發(fā)動機最高轉速可增加700rpm。
Ti-62S鈦合是金鈦金屬公司(TIMET)研發(fā)的Ti-6Al-4V的替代鈦合金。Ti-62S(Ti-6Al-1.7Fe-0.18O2-0.1Si)性能接近于Ti-6Al-4V,添加Si 可增加強度;添加鐵可降低原料成本,亦能促進晶粒細化,進而提高強度,同時改善加工性;添加O2可強化鈦合金。由于生產(chǎn)成本較低,因此價格較Ti-6Al-4V 便宜10%~20%。
鈦合金連桿的制造法一般為鍛造法,但因鍛造材料步留率低、切削性較易切鋼差及鍛造物需要酸洗除去表層之氧化物的關系,導致加工成本很高。所以目前鈦合金連桿的制造趨勢朝向凈型鑄造法及粉末冶金制造法。這兩種方法所獲得的工件在疲勞性質上已有重要的改善。
2、氣門
進氣門(Intake Valve)工作溫度約300~400℃,排氣門(Exhaust Valve)工作溫度約600~800℃,因材料需具有抗熱性,尤其是在高溫下,必須保持其強度、硬度而不燒蝕。所以具有高溫耐氧化性及耐高溫潛變的鈦合金是合適的材料。就目前的應用而言,進氣門的材料以Ti-6Al-4V 為主,排氣門的材料以Ti-6Al-2Sn-4Zr-2Mo-0.08Si(Ti-6242S)為主,Sn和Al通常一起添加,可以得到較低的脆性和較高的強度。添加Mo可增加鈦合金的熱處理性能,增加淬火鈦合金的強度,同時增加硬度。由于形狀簡單和小巧,所以機械加工是容易制造的,成本也便宜。不一定需要進行特殊的表面處理,和鋼制的氣門座相比,能減輕10~12g。
福特汽車(Ford)的一項研究報告指出,在一個四缸八氣門、1.9 L的發(fā)動機中使用鈦合金氣門,氣門質量可減少原鋼氣門質量的48﹪;發(fā)動機氣門振動的臨界轉速可提高650r/min;氣門彈簧負荷減少約30%;因氣門機構摩擦損失減少,在油耗表現(xiàn)上,平均每升汽油可增加4.3km的里程數(shù)。其他具有發(fā)展?jié)摿Φ暮辖鹩校?/p>
1)進氣門可采用Ti-62S,其特性相當于Ti-6Al-4V,且價格較便宜。
2)排氣門可采用Ti-6Al-2Sn-4.0Zr-0.4-Mo-0.45Si(Ti-1100),因為Mo含量較低,故其耐潛變抵抗性較Ti-6242S 優(yōu),耐氧化溫度可達600℃(1100°F)。此合金正由美國賽車零件制造商評估中,應用性指日可待。
3)排氣門可采用γ- TiAl。 γ- TiAl 具有耐高溫及質量輕的特點,但不適合以傳統(tǒng)的鍛造法加工,僅適合使用鑄造法與粉末冶金法加工。當制造方法更加成熟后,其價格也許會較目前廣泛使用的鎳基超合金排氣門便宜。
3、氣門彈簧座
氣門彈簧座必須具備高強度及耐疲勞性,對于耐高溫的要求不像氣門那么高。β鈦合金為熱處理型合金,能依固溶時效處理來獲得很高的強度,所以Ti-15V-3Cr-3Al-3Sn 與Ti-15Mo-3Al-2.7Nb-0.2Si 是合適的材料。三菱汽車(Mitsubishi)在其量產(chǎn)汽車上使用Ti-22V-4Al 鈦合金氣門彈簧座。質量較原鋼制鎖扣減輕了42%,氣門機構慣性質量減少6%,發(fā)動機最大轉速增加300r/min。
4、氣門彈簧
氣門彈簧的作用是使氣門能確實的關閉,尤其是發(fā)動機在高速運轉時,氣門彈簧因運動速度加快,易引起彈簧之諧振而導致氣門開閉不確實,影響發(fā)動機性能,故氣門的材料須具備質輕、強度大及耐疲勞的特性。鈦合金質量輕、比強度大及剪力模數(shù)低,是彈簧的理想材料。圓筒圈狀壓縮彈簧負荷與變形量之關系式如下:
δ=(8ND3/Gd4) P
式中δ為彈簧變形量,D為彈簧直徑,d為線徑,G為剪力模數(shù),P為彈簧負荷,N為彈簧圈數(shù)。
因鈦合金的剪力模數(shù)G 較小會使彈簧在受負荷時變形量增加,為了避免這種情形,可使彈簧在設計時有較少的圈數(shù)及縮小彈簧直徑,如此不但可減少彈簧的變形量,而且尺寸大小僅是鋼彈簧的一半,彈簧質量僅為鋼彈簧的一半。彈簧質量一減輕,便可提高共振頻率,提高發(fā)動機氣門彈簧諧振的臨界轉速,增加發(fā)動機高速運轉之效率。對汽車設計者而言,鈦合金彈簧尺寸較小,在空間的應用上會更靈活。
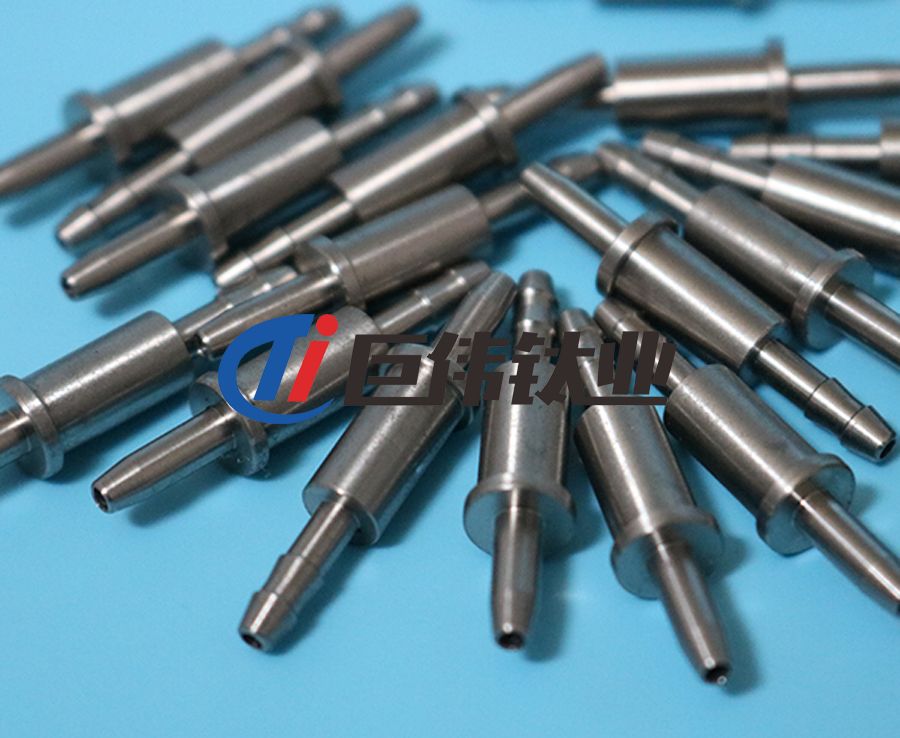
β鈦合金因具有高強度及良好的冷加工成型性,所以是氣門彈簧的優(yōu)良材料。一般在商業(yè)上使用最多的β鈦合金是Ti-3Al-8V-6Cr-4Mo-4Zr(Ti-38644)。
5、渦輪增壓器
使用渦輪增壓器可以改善發(fā)動機的燃燒效率并增進發(fā)動機功率及扭力。然而,渦輪增壓器的輪機轉子(turbine wheel)長期暴露在850℃以上的高溫廢氣中,故具備耐熱性是很重要的條件。傳統(tǒng)的輕金屬,如鋁合金或鎳基合金,因其溶點較低,無法使用。雖然陶瓷材料質量輕且耐高溫性佳而被應用在輪機轉子上,但由于成本高及形狀上無法最佳化而使得應用上受到限制。因此Tetsui 等人發(fā)展了TiAl 輪機轉子,經(jīng)過了多次的發(fā)動機試驗,不但其耐久性及效能已受到證實,而且也可以改善發(fā)動機加速性及減少廢氣中的有害物質。此項設計已成功的商業(yè)化應用在Mitsubishi LancerEvolution 系列車款上。
6、排氣系統(tǒng)
鈦合金因為具有良好的耐蝕性,故很適合做為排氣管(含消聲器)的材料。因耐蝕性佳,故排氣管的管壁可以作得較薄,約1mm 厚,所以鈦排氣管與不銹鋼排氣管比較起來,可減輕約60%的質量,例如409 不銹鋼排氣管重達10kg,但鈦排氣管質量只有3.2kg。商業(yè)用純鈦(CP)是排氣管的理想材料,ASTM Grade 2之純鈦(如Timetal50A)在取得性、制造性、焊接性與機械性質上是很合適的材料。純鈦可于冷溫下成型,所以鈦排氣管適合于在室溫下成型,且其成型的設備與技術皆和鋼排氣管相同,這使得鈦排氣管在制程上的成本并不會增加。鈦排氣管的制程是利用縫焊與電阻焊將膨脹箱(expansion box)焊合,然后再使用惰氣金屬極電弧焊(gas metal arc welding , GMAW)或惰氣鎢極電弧焊(gas tungsten arc welding , GTAW)將排氣管與膨脹箱焊接起來。
7、其他鈦合金部件
鈦合金在車輛中廣泛應用,能大大消減整車質量和提高耐用性,發(fā)動機元件,驅動齒輪系零件、懸掛系統(tǒng)和結構件、車體框架等來講都可用鈦合金取代鋼。如發(fā)動機搖臂、緊固件、車擋支架、制動器卡鉗活塞、銷軸栓、離合器圓板、壓力板、控制桿、從動軸、閥彈簧和緊固件等。
二、鈦合金零部件的優(yōu)越性
鈦合金具有質輕、比強度高及耐蝕性好等優(yōu)點,在汽車工業(yè)中得到了廣泛的應用,應用最多的是發(fā)動機系統(tǒng)。鈦合金零部件的應用可減少發(fā)動機振動與噪聲,提高曲軸轉動速度,減少曲軸應力,得到較高的發(fā)動機扭力,可提高發(fā)動機氣門振動的臨界轉速,可減少彈簧負荷,減少氣門機構磨損及降低燃油消耗。
在汽車的消聲器設計、制造及應用是合適的,一方面利用鈦合金室溫下的高加工性,同時也提高應用高溫強度、高耐氧化性及耐蠕變性。鈦合金在其他部件上的應用可提高人員的舒適度和汽車的美觀等。另外鈦合金在汽車節(jié)能降耗方面起到了不可估量的作用。
結語
鈦合金應用在汽車上已經(jīng)有良好的效果,但目前多應用于賽車及跑車上。價格昂貴與制造成本高是鈦合金不能普遍應用在家庭房車的根本原因。所以,低價鈦合金的開發(fā)是鈦合金實用化的重要關鍵,以下幾點是今后鈦合金零部件開發(fā)應用的方向:
1)以低價格的添加元素取代鈦合金中重要的添加元素如V、Mo 及Nb 等高價元素。
2)開發(fā)易切削之鈦合金。
3)改善制造鈦粉末的方法。
4)使用連續(xù)鑄造法生產(chǎn)小直徑鈦棒或平板,可減少人力及能源的運用,降低成本。
5)采用近凈型(near net)鑄造技術或近凈型粉末冶金制程開發(fā)低價鈦合金。
我國正在大力開展汽車用鈦的推廣工作。逐漸將鈦與汽車聯(lián)系起來,以促進鈦在汽車方面的應用。而汽車用鈦研究工作則一直在展開,如粉末冶金鈦和TiAl的研究。鈦合金價格昂貴主要是受制于目前的冶煉加工技術,而鈦在地殼中的半富程度僅次于鋁、鐵、鎂,排第4位。由于鈦合金工業(yè)不斷的在民用產(chǎn)品上的開發(fā)應用,鈦合金的產(chǎn)量也逐年增加,對鈦合金技術的研發(fā)也必將得到進一步加強,鈦冶煉及加工成本的降低也是必然趨勢。因為鈦合金在實現(xiàn)汽車輕量化、低燃油消耗率及高性能上的表現(xiàn),全球范圍內節(jié)能減排的要求、新能源汽車篷勃發(fā)展,簡化制造工藝內在降低成本,是未來汽車發(fā)展趨勢,所以鈦合金必將在汽車工業(yè)中占有重要的地位,得到廣泛應用。鈦合金部件在普通家用汽車上的應用在不久的將來必將得到廣泛應用。
參考文獻
[1] 李修明,趙成龍,齊萌蒙.面向數(shù)字化工廠建設的數(shù)據(jù)應用研究[J].數(shù)字技術與應用,2020(5) : 70-73.
[2] 劉亮.數(shù)字化工廠的實現(xiàn)方式與應用分析[J].經(jīng)營者,2019(4):123-125.
[3] 田建忠.數(shù)字化工廠應用現(xiàn)狀與前景展望[J].創(chuàng)新科技,2017(5):36-38.
相關鏈接